By Brad Fuller
Rich Thomason is resolute in his belief that mass timber is not only an attractive, aesthetically stimulating building option, it also has major long-term environmental sustainability upside, despite current estimates that peg it as driving overall building costs up at least 10%.
“Mass timber is a noble endeavor for construction—if you’re trying to just pencil it out and do it for cost, we’re not there yet,” said Thomason, Owner of Ogden-based Timber Works, a framing services contractor. “If you do think climate change is a real thing that needs to be addressed, and do care about the planet, mass timber is a small way for us builders and contractors to contribute to that endeavor.”
Thomason’s firm is on the frontlines of the rising tide of interest in mass timber construction, having done the installation of CLT beams, columns, and panels on a range of notable projects the past seven years, including recently on Utah’s first full-scale mass timber project, Baltic Pointe in Draper.
The all-electric, 136,000 SF, five-story (plus two underground parking levels) building has a majestic location perched on a hill east of I-15 overlooking to the west The Point development and will undoubtedly serve as a beacon for the mass timber market upon on its expected Q4 completion this year.
Baltic Pointe is a venture between Salt Lake-based Gardner Group, its subsidiary Philo Ventures of Lehi, Celtic Bank, and Pelion Venture Partners of Salt Lake, which will move its headquarters to the top two floors and have the company’s name on the crown of the building. HB Workplaces (formerly Henriksen Butler) will be another anchor tenant with its headquarters and showroom spanning the entire first floor.
Representatives from the development team are bullish about several inherent benefits associated with mass timber and believe premium up-front costs will be mitigated by value engineering, shrewd design strategies, and the ability for owners to extract top-shelf lease rates.
“We believe in using state-of-the-art technologies and building materials to reduce our building impact to the environment,” said Christian Gardner, CEO of Gardner Group, citing statistics from various sources that claim mass timber can achieve true net zero impact via sustainable harvesting and processing. “Part of Gardner’s mission is to discover more sustainable ways to build. To do this, we need to venture from the status quo and embrace new innovations and building materials. This building will be the first commercial project in Utah to be built with mass timber, and we are optimistic that it will be the first of many.”
“We think the benefits of the prefabrication process of mass timber—compared to traditional steel and concrete construction methods—will see an offset of cost from the rising rates of labor, making mass timber more cost effective,” added Ryan Bevan, the firm’s President of Construction. “Our hope is that Gardner sets a new precedent in Utah for prioritizing the use of renewable natural resources in construction.”
Microsoft Tour Sparks Mass Timber Interest
According to Marbe Agee, Principal-in-Charge at Salt Lake-based Method Studio on Baltic Pointe, initial interest in mass timber was sparked during the design of Zions Bancorp’s Technology Campus project, which was developed by Gardner and designed by WRNS (core and shell) and Method (interiors). The three firms each sent reps to California in February 2020 to tour Microsoft’s newest addition to its sprawling, 32-acre campus in Mountain View, a 644,000, highly sustainable Class A office building that is the largest Cross Laminated Timber (CLT) structure in North America.
Method quickly assembled a “Mass Timber 101” report for Gardner on how CLT and glulam products might pencil on a spec office building, and the project gained traction post-Covid when Gardner and Pelion decided to partner on Baltic Pointe.
Christian Gardner said after the Microsoft tour his firm “started our own research with a few local and national design teams and mass timber consultants. I wanted to explore mass timber structures both for their uniqueness in the market and as a more sustainable alternative to steel and concrete.”
“In many ways, building using this new technology embodies our vision as a company,” said Blake Modersitzki, Managing Partner at Pelion Venture Partners. “We value creation, vision and positive disruption as we build successful communities, and Gardner Group has been an amazing partner to work with as we embrace this innovation.”
Baltic Pointe also serves as a pilot project for Philo Ventures, a Utah-based start-up company that Gardner has a stake in. According to CEO Chad Staheli, the firm has been looking at “trying to pencil out and value engineer an industrial (mass timber) building, and we’ve been able to make some cool findings. We’re just a hair off (sub 8%) concrete tilt-up. We’ve been hyper-focused on industrial and mass timber as a replacement for concrete tilt-up, as well as multi-family. It works particularly well in the 8- to 12-story category with the new IBC code.”
Staheli said the firm is even contemplating getting into the mass timber manufacturing arena, depending on how quickly developers in Utah and the Intermountain region respond to the market.
“We have to get a few projects under our belt (as a market),” said Staheli. “We think if we can get some early wins, both on the industrial and multi-family side, it will have […] a spreading influence. You have to show on these non-sexy applications that the economics work out, but there is a premium people are willing to pay to participate in real sustainability. Our research is focused on leveraging innovative design and manufacturing processes to achieve price parity with traditional construction methods, making it more economically feasible to bring the benefits of mass timber to a broader range of projects.”
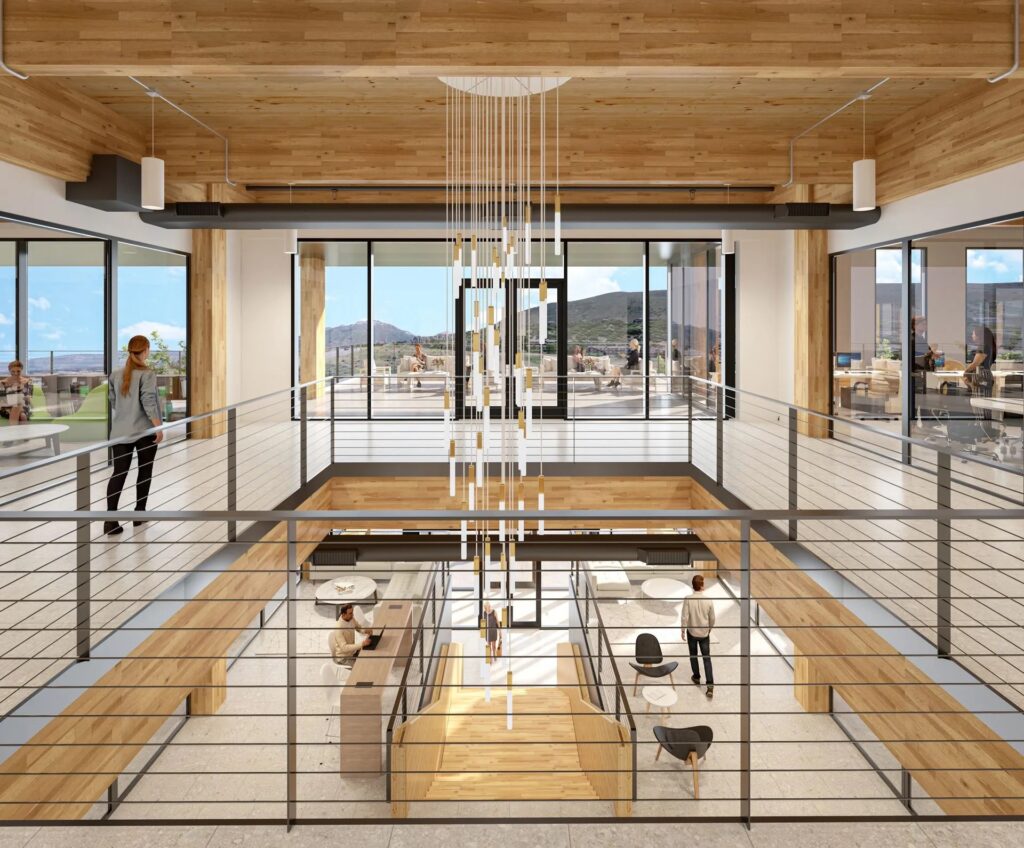
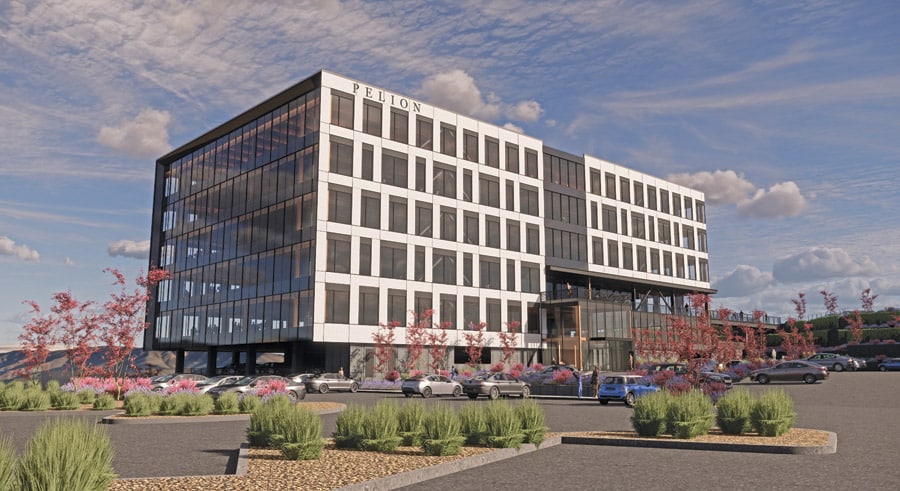
Benefits of Mass Timber
Mass timber is a class of wood products made by tightly layering soft lumber boards to create columns, beams, and panels. The products are strong enough to replace steel and concrete in load bearing applications and are slated to be approved for buildings up to 18 stories under the International Building Code (updates are pending).
Structurally, there is confidence in mass timber measuring up well vs. concrete and steel, although there are areas of concern regarding strength and durability that require specific design considerations, which can be overcome for most buildings, said Brett Goodman, Principal for BHB Structural Engineers of Salt Lake.
“Utilizing mass timber in Baltic Pointe brings unique engineering challenges and opportunities,” said Goodman. “Integrating mass timber systems requires careful consideration of load-bearing capacities, fire resistance, and dynamic performance. Collaborating with architects and other engineering disciplines, we optimized the structural design to ensure the building’s safety, durability, and long-term performance. For the building’s seismic design, we kept the high performance of a steel buckling restrained brace frame system (Core Brace) and tied that into the mass timber structure. This was a unique solution that fit the needs of Baltic Pointe.”
The floors of Baltic Pointe are comprised of massive Cross Laminated Timber (CLT) panels measuring 5 in. thick by 10 ft. wide by up to 60 ft. long. The CLT is made by “laminating” layers of standard 2×4 to 2×10 members with glue similar to glulam beams. Each layer “crosses” by stacking them perpendicular to the last—the result is one large, stiff wood member that makes for a great floor.
Current testing—funded by the U.S. National Science Foundation—is being done via the Natural Hazards Engineering Research Infrastructure (NHERI) TallWood project, which aims to investigate the resilience of mass timber high-rise buildings by simulating a series of large earthquakes on a full-scale, 10-story mass timber building. Seismic testing is being led by professors from the Colorado School of Mines and University of Nevada, Reno (UNR).
“Resilient design must also account for the building’s nonstructural systems, which are not part of the structural load-resisting system but play an important role in the building’s function and its ability to recover after the earthquake,” said Keri Ryan, project co-investigator and UNR engineering professor.
Approximately 1,500 mass timber projects have been constructed or are in design in the U.S., although few exist in the Intermountain West. Mass timber is largely prefabricated off-site and pieced together like a giant puzzle, so it can facilitate shorter construction times and be completed by a smaller labor force.
Mass timber also aids in reducing construction schedules because “with this kind of construction, as soon as we get the structure up, we don’t have to pour decks and fireproof beams—we can start right in with framing and MEP rough ins,” said Eric Barton, Project Executive on Baltic Pointe for Salt Lake-based Okland Construction, which is also building Millcreek City Hall.
Thomason said installation of mass timber requires a delicate touch, a process Timber Works has been refining since it installed all the mass timber in the Star Mill project in Alpine in 2015. On that project, Thomason said the mass timber fabricator out of British Columbia was “expensive, did poor quality, hard to work with […] and once we got the product installed, we thought we should have just (fabricated it) ourselves.”
That has evolved into Timber Works offering full-service mass timber fabrication and installation, developing a reputation as a contractor who understands the trade. “I’m vested in the market,” said Thomason. “We buy the steel, timber, framing, and offer a turn-key package to our clients. It’s a better way to build.”
Perhaps the most important benefit—and the one underlying factor that ultimately moves the needle on this market—is the carbon footprint reduction vs. steel or concrete, which are well-known contributors to global CO2 emissions.
According to statistics from 2022, cement and steel production accounts for approximately 11% to 15% of all global CO2 emissions, a major driver of climate change. Replacing these traditional building materials with CLT mass timber would naturally reduce CO2 levels; the use of mass timber on Baltic Pointe reflects a decrease in carbon impact equal to taking more than 1,500 cars off the road for a year or powering 780 homes for a year with renewable energy.
When forests are managed sustainably, wood is a renewable resource and easily sourced in North America. For perspective, it takes about 16 minutes for the wood used in Baltic Pointe to be collectively grown in existing U.S. and Canadian forests.
Other positive factors include mass timber’s high strength-to-weight ratios and natural flexibility, which enable excellent performance during seismic activity. CLT columns and panels also meet or exceed fire code requirements. During a fire, exposed wood chars on the outside, forming an insulating layer that protects the interior from damage the same way redwood trees survive fires.
Mass timber’s aesthetic and environmental appeal are market differentiators that increase a project’s value and lease rate. Research indicates that when people are surrounded by natural materials, it lowers their stress response and improves cognitive function.
On Millcreek City Hall, nature and the community were driving ideas behind incorporating mass timber elements into this dynamic new building, according to Ryan Wallace of Salt Lake-based MHTN Architects. Approximately 12,000 SF of the total 76,000 SF project is constructed of mass timber, including CLT posts, beams, and panels. The rest of the structure is comprised of low-carbon concrete, making for a greatly reduced carbon footprint.
“The potential impact of mass timber construction to de-carbonize the built environment is thrilling to our team and aligned well to Millcreek, a forward-thinking community sensitive to living their motto of being ‘connected by nature’,” said Wallace, adding that it will likely take some time for other public (and private) owners to embrace mass timber.
“Not all owners fall into the category of early adopters willing to take the chance on this re-emerging construction method,” said Wallace. “Completed projects, with more predictability of cost, procurement, and quality of construction […] will be important for the next wave of owners to consider.”
Market Outlook
Jake Gines is an Associate Principal at Method Studio, who also happens to be a Professor at Mississippi State University’s School of Architecture—he racks up a slew of airline miles commuting between Salt Lake and Starkville during the school year—a position he’s held for 11 years. He has been teaching mass timber studios for most of his tenure and believes the CLT market is primed for significant growth, despite the typical cautious approach by owners.
“It’s exciting to see a lot of movement in the market,” said Gines. “It’s the classic chicken and egg thing, where we’re not going to supply something until there is a demand. It’s been on a slow burn for years.”
Gines mentioned new U.S. government grants as helping to generate more interest and activity, but there needs to be even more incentives and additional research into mass timber’s long-term viability as an affordable competitor to steel and concrete.
“The gap will close as we understand the material better, get better with engineering, and as more products come along, we can have a more competitive environment,” Gines added. “Even though [mass timber] projects cost more, when you look at the material, I think [projects] are very cost competitive. Baltic Pointe is a perfect example of a great team […] all coming together to create a fantastic project and make some hard decisions on what we can and can’t do to make it pencil.”