Digging Deeper | Mass Timber
A perfect combination of client and project encouraged the developer to green-light innovative building technology
By Brian Fryer
May 23, 2023
From a distance, the new Baltic Pointe office building rising on the foothills of Draper about 20 miles south of Salt Lake City doesn’t appear much different from others populating Utah’s tech corridor, known as the Silicon Slopes. But up close and inside, its look, feel and particularly the smell of Douglas fir make it noticeably different from traditional steel and concrete constructions. The first mass timber commercial building in Utah, Baltic Pointe is causing a stir among developers and sparking curiosity in the region’s construction and design community.
“We’ve never had so many requests for tours of a building before,” says Liza Hart, senior development manager and vice president for sustainability with Baltic Pointe’s developer, Salt Lake City-based Gardner Group.
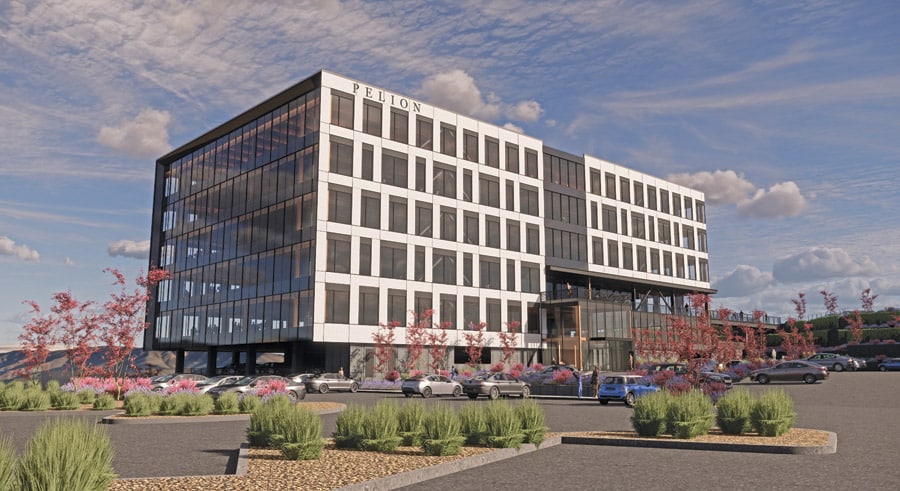
Image courtesy of Method Studio
Fossil Fuel Reduction
The $32.5-million, 130,000-sq-ft, five-story office tower sits on a two-level, above-grade parking garage. It occupies a five-acre triangular slice of mountain foothills with views of the wider Salt Lake Valley.
Building with mass timber elements like cross-laminated timber panels (CLT) or glulam beams and columns has been growing in popularity as owners and builders look for ways to reduce the environmental impacts of construction projects. Groups like the World Economic Forum estimate building construction and operation account for about 40% of global CO2 emissions. Mass timber construction eliminates the fossil fuel impact of producing traditional construction materials like steel and concrete. Trees used to create mass timber components remove CO2 from the atmosphere as they grow and sequester the carbon for the life of the wood product, effectively removing it from the carbon cycle, potentially for decades.
“I think people are falling back in love with wood…. It can help create a unique, comfortable work environment.”
—Jake Gines, Method Studio
“Because of the efficient mechanical systems and the building envelope we have, we estimate this building is 52% more energy efficient than a typical office building in Utah,” Hart says. The building is all electric with heating and cooling to be done by a variable refrigerant flow (VRF) system.
Christian Gardner, Gardner Group’s chairman and CEO, “really became more aware of mass timber buildings and got excited about them around 2020,” Hart notes. Gardner asked Method Studio to do feasibility studies and “then it was just a matter of having the right project and client and place come along.”
The technology venture capital group Pelion, based in Cottonwood Heights, east of Salt Lake City, partnered with Gardner on the project and will move its headquarters into the top three floors of the completed building. The offices and showroom of Salt Lake City-based office furniture retailer HB Workspaces (formerly Henricks and Butler Design) will occupy the lower two floors.
Bevan, president of construction for Gardner Group, says the costs for this mass timber project have been higher than those for a building constructed using traditional steel and concrete. Parking requirements and the site’s size dictated building a parking garage, and this prevented the developer from realizing savings that can come with smaller footings and slabs needed for mass timber buildings due to their reduced weight. But Bevan says other factors made the project worth doing.
“Class A office market is struggling, and people are looking for ways to lure workers back to the office,” Bevan says, noting that demonstrating a commitment to sustainability and creating a comfortable, unique work environment could be a draw for some workers.
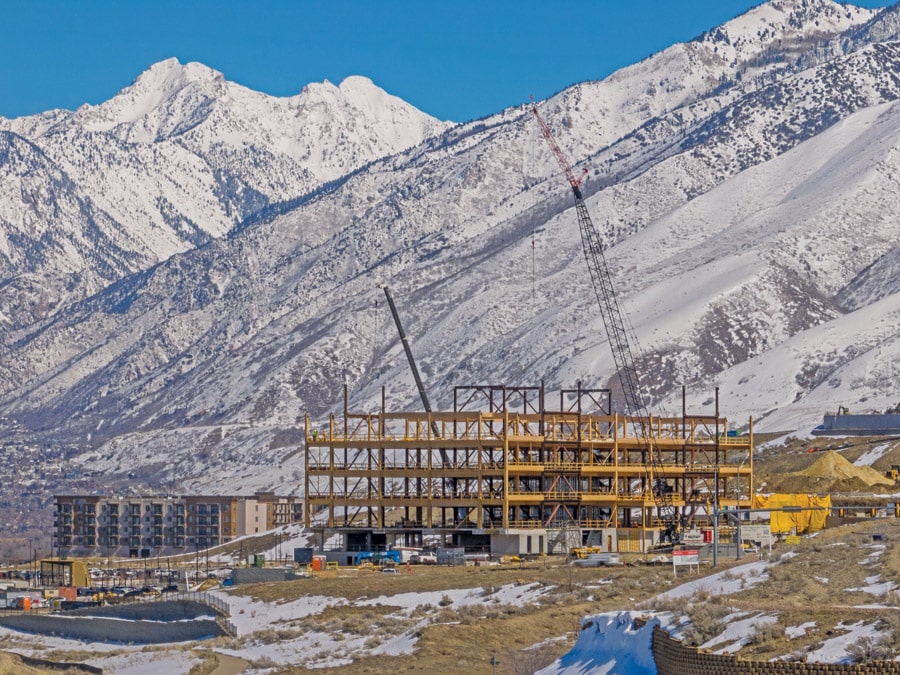
Image courtesy of Gardner Group
Lumber and Learning
Designer Jared Wright, vice president at Method Studio, and Eric Barton, project manager for Salt Lake City-based general contractor Okland Construction, worked closely with mass timber supplier Kalesnikoff of British Columbia, which also performed design-assist on the CMGC delivery project. Kalesnikoff fabricated the components at its facility in Canada and shipped them to the site. Each piece is marked as to where it should be placed, then lifted into position and bolted in place.
“We’ve learned a lot on this for sure,” Barton says. “We’ve done projects that had some mass timber before but nothing like this. There is not a lot of special equipment needed. We had the hangers for the beams installed on the columns at the factory and the CLT for the floors just screws in place.”
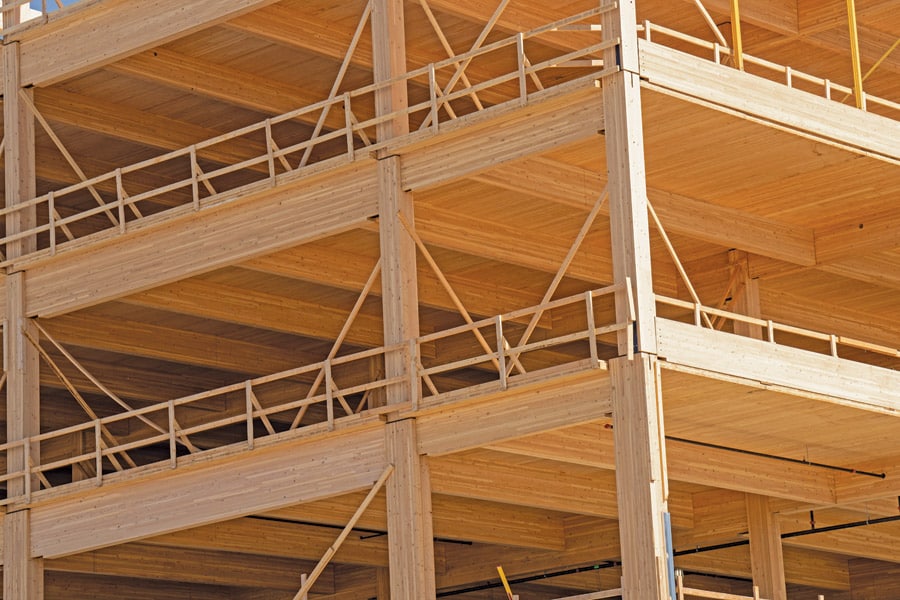
Image courtesy of Okland Construction
The building’s location is notorious for strong winds—a world class hang-gliding park is located on the hills above the site—and Bevan says that created a challenge when lifting the large CLT floor panels, some of which were as large as 12 ft by 50 ft.
While mass timber components are the primary structural system for the building, to meet seismic codes, the perimeter of the building includes four sections, two on the east side and two on the west, of full-height steel columns fitted with buckling restrained braces (BRBs). Three more bracing systems are inside the building, around the elevator and utility core and the central stairway.
Travis Brackus, CEO and principal at Salt Lake City-based structural engineering firm BHB, Baltic Pointe’s engineer-of-record, says the team did consider the possibility of having shear walls made from timber rather than using BRBs. “But shear wall systems built from CLT panels start to get really large and restrict your flexibility with the office space. The brace system on the perimeter won’t inhibit the windows and daylight and the views. It was a challenge marrying those two systems together. But Kalesnikoff offered some great guidance on connections, and between them and feedback from Okland, we got a system that works.”
says the parking garage at the base posed another challenge since the structural columns in the building needed to line up with those in the garage.
“We ended up with a 30- by 30-foot grid, which is very easy to do with steel but is a lot more challenging with wood because that is a long span,” he says. “Kalesnikoff was great to work with to get the right pieces engineered.”
Another peculiarity of working with mass timber is accounting for how well it would perform in a fire, and the structural integrity of the components needs to be calculated twice.
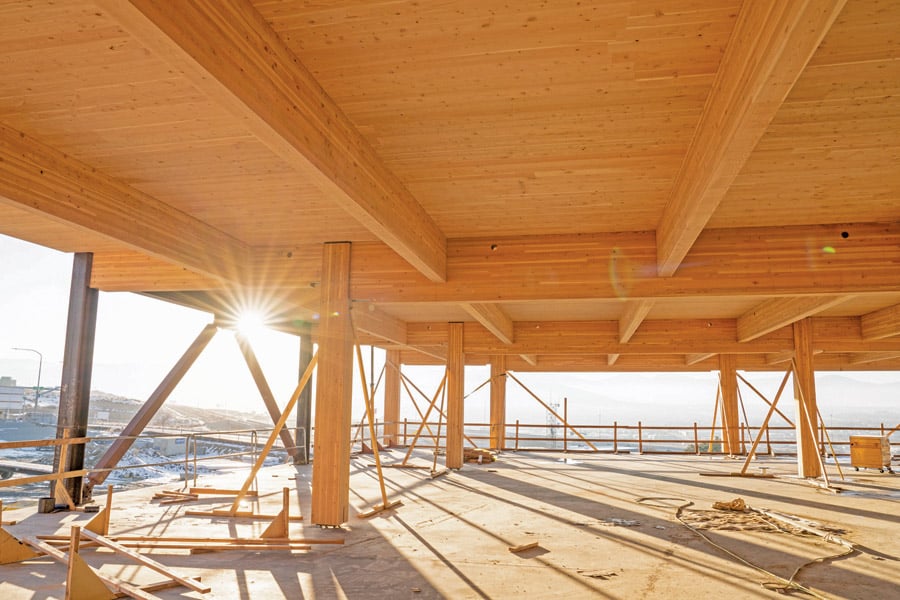
Image courtesy of Okland Construction
“We do calculations for the size of the columns and beams when the full, live load is on,” Brackus says. “Then we do a secondary calculation where we assume fire conditions, burning for one to two hours, and you determine the size you need.”
The 2-ft x 2-ft square columns are 14 ft high, though the thickness decreases slightly as the building gets higher and there is less weight to carry. The three-ply CLT floor panels are just over 4 in. thick, while the beams they rest on measure 36 in. x 20 in. and span up to 30 ft.
Wright says the floor panels will be covered with a thin top coating, but other than that, the wood will be exposed on the interior. The building will have EFIS (exterior insulation finishing system) cladding.
The exposed wood is a key feature of the interior, and Wright says the design team had to be meticulous about how the exposed electrical and plumbing lines would be installed.
“The fire sprinkler pipes are the only things that penetrate the beams on the ceilings,” he says. “We’re working with the trades to keep the wiring and pipes up against the beams. They have to keep in mind how visible it will be.”
The project broke ground in July of 2022, with completion expected near the end of November.
Developing a Taste for Timber
Baltic Pointe developer says project likely first of more to come
By Brian Fryer
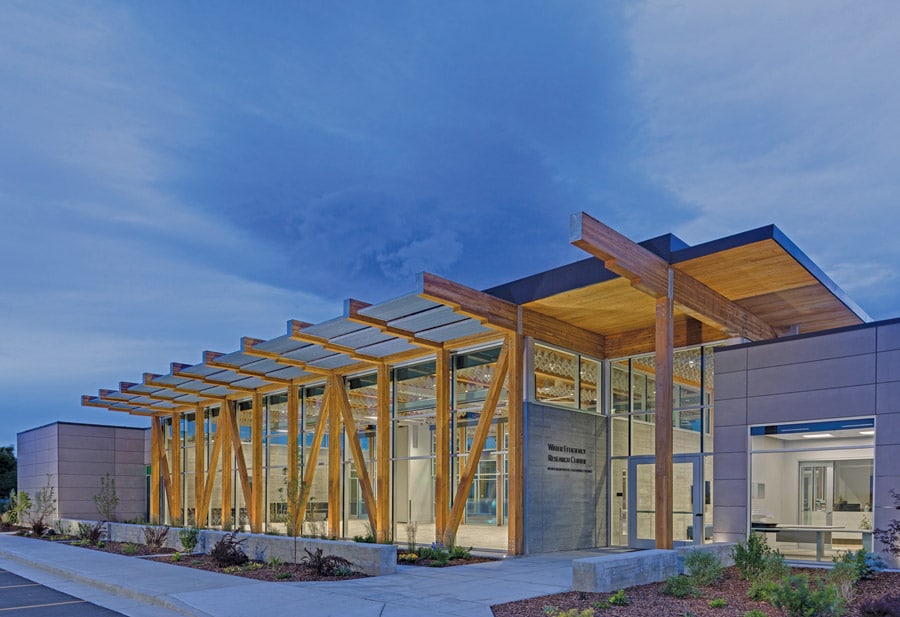
Image Courtesy of GSBS Architects
While many members of the Baltic Pointe building team had experience with different aspects or components of mass timber buildings, they had not put everything together on one project before. “We want to be thought leaders on this and see more developers do this too. We’re all learning a lot here,” says Lisa Hart, senior development manager and vice president of design and sustainability for Salt Lake City-based Gardner Group, the developer of Baltic Ponte.
Jake Gines, associate principal at Salt Lake City-based Method Studio, the Baltic Pointe design firm, is also an associate professor of architecture at the University of Mississippi, where he directs the mass timber studio. He says interest in the technology across the U.S. is rising for several reasons.
“It opens another option for design. It is a familiar and natural material,” he says. “I also think people are falling back in love with wood. There is just a different feel about it, and it can help create a unique, comfortable work environment.”
In recent years, mass timber has featured prominently in buildings in the Intermountain Region, like the Idaho Central Credit Union Arena at the University of Idaho, the Weber Basin Water Conservancy District (WBWCD) offices in Layton, Utah, and the new Millcreek City Hall for the municipality in the Southeast Salt Lake City metro area.
The reasons for choosing to build completely with mass timber or to opt for a hybrid design with major mass timber elements varies widely. Architect Jeff Bolinger with Salt Lake City-based GSBS Architects was part of the design team for the WBWCD offices and is a mass timber proponent. He says while initial costs for building entirely with mass timber are higher, there are other factors to consider.
Bolinger said mass timber can differentiate a building in the marketplace. Baltic Pointe project partner Pelion Venture Partners not only wanted proximity to technology start-ups in the Silicon Slopes but also a distinctive and environmentally conscious building for its new headquarters, and the venture capital firm was willing to pay a premium for it. Bolinger said in the case of the WBWCD building, district officials chose to incorporate mass timber to reflect and support their mission of environmental conservation and education.
“There can also be reduced construction costs because mass timber gets produced off site and then shipped. You don’t need as many people on site, usually just a crane and a crew to secure the pieces in place. You have a less busy and cleaner worksite,” Bolinger says.
In a recent article on mass timber for the Utah Chapter of the American Institute of Architects, Bolinger cites studies that estimate time savings of up to 25% using mass timber compared with steel and concrete. Mass timber buildings often require less concrete for footings and slabs due to the reduced weight of the structure.
Hart says new financial incentives are also lowering the cost for developers of mass timber projects.
“The Inflation Reduction Act has incentives for embodied carbon, and those are still being worked out by the IRS but should be out soon,” Hart says. “There is also more advantageous funding emerging. Wells Fargo just announced they will have a $500-billion fund for sustainable projects, and if you can meet the criteria they are developing, you can take advantage of that. Couple that with things like rebates from utility companies, grants from places like the U.S. Forest Service, and we think there are ways to use [mass timber] in more and more cases.”